Lekki, modularny samochód miejski o napędzie elektrycznym
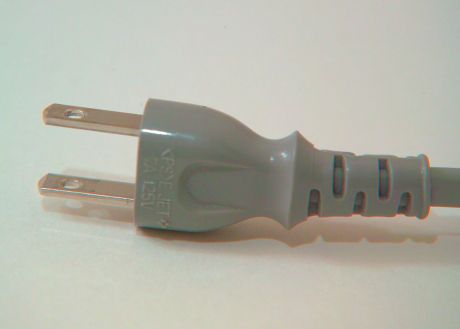
JapanesePlug
By No machine-readable author provided. Fg2 assumed (based on copyright claims). [Public domain], via Wikimedia Commons
Jesteśmy coraz bliżej opracowania w pełni elektrycznych pojazdów dzięki innowacyjnej architekturze surowego nadwozia ze stopów aluminium i materiałów kompozytowych.
unktem odniesienia dla prac projektu EVOLUTION (The Electric Vehicle
revOLUTION enabled by advanced materials highly hybridized into
lightweight components for easy integration and dismantling providing a
reduced life cycle cost logic) jest koncepcja samochodu Pininfarina
Nido. Dotychczasowa koncepcja surowego nadwozia (BiW) została całkowicie
przemodelowana przy użyciu strategii projektowania obniżającej liczbę
elementów i korzystającej z technologii innowacyjnych, lekkich
materiałów.
Wybrany archetyp nadwozia z komorą centralną jest skonsolidowanym standardem, uwzględniającym schemat procesu montażu, pozwalającym łatwo zwiększać skalę produkcji. Komora ma przede wszystkim funkcję strukturalną, przód ma kształt umożliwiający absorbowanie energii podczas zderzenia czołowego, a tył został opracowany w formie modularnej, umożliwiającej przekształcenie w wersję van lub pick-up.
Rozważane technologie Al zastosowane w przypadku stopów Al 5xxx-6xxx i 7xxx umożliwiają otrzymanie części o skomplikowanej geometrii i niewielkiej grubości oraz łączenie różnych części w jeden, unikalny element. Umożliwiają też przetwarzanie danego elementu w pojedynczej operacji przy zmiennej grubości.
Technika formowania na wilgotno umożliwia jednoczesne odlewanie połączeń między różnymi elementami uzyskanymi w różnych procesach produkcyjnych.
Potencjalne ograniczenie kosztów oraz uproszczenie i skrócenie procesu montażu to obiecujące możliwości: bieżący stan wiedzy, korzystający z tradycyjnych metod odlewania, takich możliwości nie daje.
BiW w niektórych obszarach podwozia stanowi hybrydę z materiałem kompozytowym z grupy PA, wzmocnionym przez GF. Taki materiał uzyskano poprzez udoskonalenie dotychczas znanych materiałów i stworzenie procesu produkcji na skalę odpowiadającą wymogom komercyjnym, polegającego na zaawansowanym termoformowaniu arkuszy i wtryskiwaniu 3D (proces CaproCAST).
Innowacyjne nanokompozyty polipropylenowe (pnc) na bazie warstw krzemionki i włókna szklanego o zwiększonej sile i sztywności zostały wyselekcjonowane na potrzeby modeli demonstrujących zderzenia z belką poprzeczną i drzwiami bocznymi. Do wypełnienia absorbujących energię odcinków belki poprzecznej użyto pianek poliuretanowych na bazie polimerów uzyskanych w sposób zrównoważony: z recyklingu.
Rozważono zastosowanie strukturalnych klejów epoksydowych do łączenia elementów BiW, przez co zmniejszyła się liczba spawów: w pewnych miejscach zastosowano zgrzewanie punktowe, ale tylko do mocowania elementów podczas polimeryzacji.
Obecne prace w połączeniu z wcześniejszymi pozwoliły osiągnąć masę BiW wynoszącą 115 kg w porównaniu z 160 kg w przypadku samochodu wyjściowego. Analiza metodą elementów skończonych samochodu jako całości udowodniła, że jego zachowanie strukturalne jest prawidłowe pod względem wytrzymałości na wypadki oraz globalne parametry statyczne i dynamiczne, biorąc pod uwagę unijne wymogi dotyczące homologacji.
Innowacyjna architektura i zastosowanie lekkich materiałów zapewni utrzymanie konkurencyjności przemysłu motoryzacyjnego w UE względem Azji i USA.
opublikowano: 2015-11-23